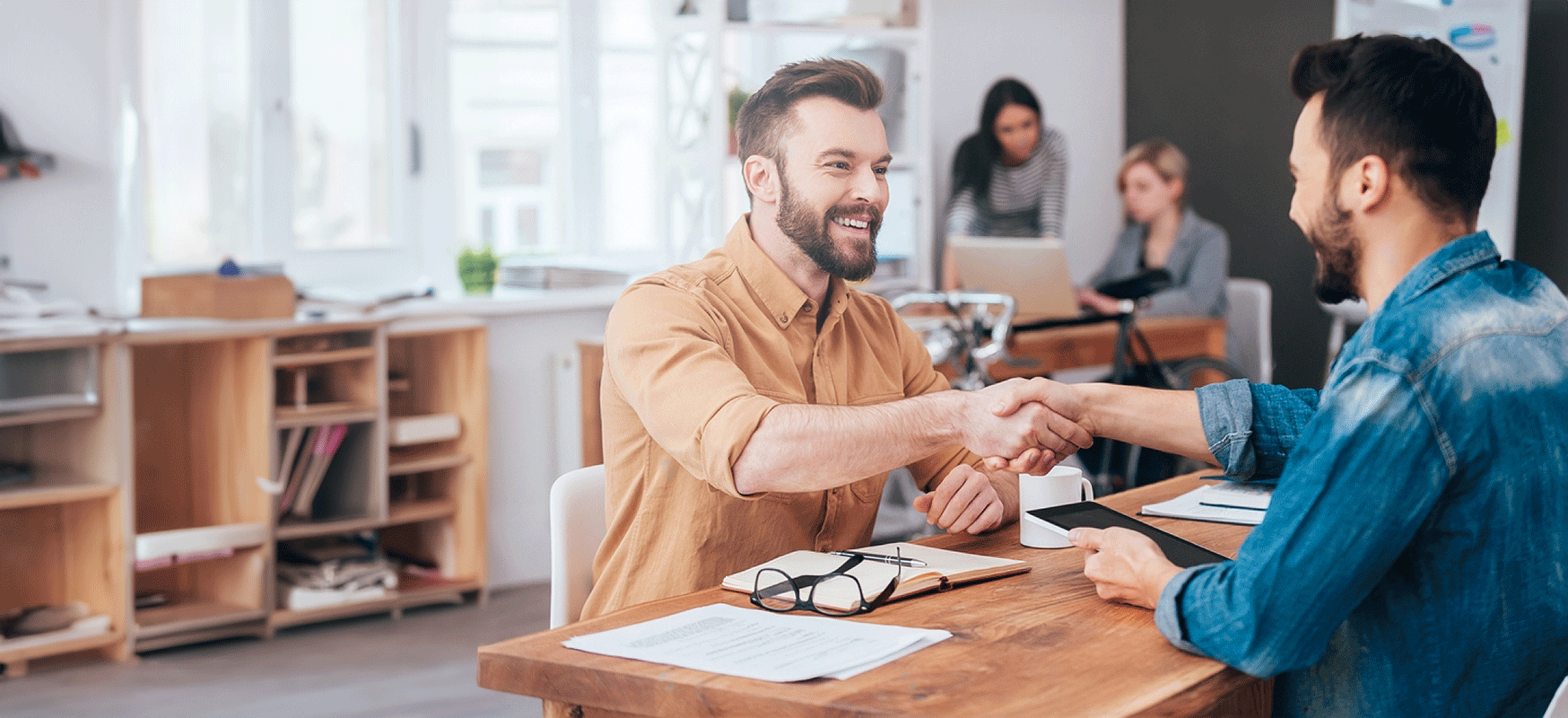
Manufacturing businesses are unique as also the manufacturing accounting. The accounting for a manufacturing business deals with inventory valuation and cost of goods sold. In other businesses, these two aspects are handled in a more simplified manner.
Manufacturing businesses use certain raw materials and convert them into finished products through various manufacturing and value-added process stages using appropriate machinery and manpower. At any given point of time, a manufacturing business has raw materials inventory, in-process or semi-finished inventory, and finished goods inventory.
Inventory valuations are done through Direct cost allocation, overhead cost allocation, and impairment testing. Indirect cost allocation, costs are arrived at through standard costs or weighted average or cost layering. In overhead cost allocation, factory overheads are aggregated into cost pools and allocated to the number of goods produced over a reporting period. In impairment testing, inventories are written down to market value.
We appreciate your interest in IMC and are eager to address your needs.
To ensure we address your needs accurately and promptly, please fill out this form. This will help us in identifying and connecting you with the appropriate team of experts in our organization.
We take pride in our responsiveness and aim to get back to you within a span of 1-2 business days. Your journey towards solutions starts here.
Companies we have worked with
© 2025 IMC Group. All Rights Reserved.
Your Partner in
Growth
175+
Countries
17,500+
Professionals
525+
Locations
2350+
Global Partners
Companies we have worked with
Speak To Our Experts
Speak To Our Experts
To provide the best experiences, we use technologies like cookies to store and/or access device information. Consenting to these technologies will allow us to process data such as browsing behavior or unique IDs on this site. Not consenting or withdrawing consent may adversely affect certain features and functions.